Cryogenic Valves and Accessories: Ensuring Safety and Efficiency in Extreme Conditions
The Role of Cryogenic Valves in Industrial Applications
Cryogenic systems store and transport extremely low-temperature gases like liquid nitrogen, oxygen, argon, hydrogen, helium, and LNG (liquefied natural gas). These gases require specialized cryogenic valves to control their flow, pressure, and safety in various industrial applications, including healthcare, aerospace, energy, and research.
Unlike standard valves, cryogenic valves are engineered to function efficiently in temperatures as low as -196°C (-320°F). They must ensure minimal gas loss, prevent leakage, and withstand extreme temperature fluctuations without mechanical failure. The unique challenges of cryogenic applications demand precise engineering and high-quality materials to prevent operational hazards such as thermal contraction, icing, and pressure buildup.
Understanding Cryogenic Valve Technology
Cryogenic valves must address several challenges specific to low-temperature environments:
- Thermal Expansion and Contraction: Metal components contract at cryogenic temperatures, requiring specialized materials and designs.
- Ice and Frost Formation: Cold surfaces can accumulate ice, affecting performance and durability.
- Vacuum and Pressure Management: Cryogenic gases expand rapidly when warmed, making pressure control crucial.
- Long-Term Durability: Valves must operate reliably over long periods to avoid frequent maintenance and downtime.
Types of Cryogenic Valves and Their Functions
Different types of cryogenic valves are used in various applications depending on flow control requirements, system design, and safety considerations.
1. Globe Valves
- Provide precise flow control and throttling.
- Feature an extended bonnet to prevent freezing of critical components.
- Commonly used in medical gas supply, LNG terminals, and research facilities.
2. Gate Valves
- Designed for full open/close operations.
- Offer minimal flow resistance, making them suitable for bulk gas storage and transport.
- Used in LNG processing, air separation plants, and large cryogenic storage tanks.
3. Ball Valves
- Feature a quick shut-off mechanism for emergency situations.
- Include extended bonnets for thermal insulation.
- Ideal for both high- and low-pressure cryogenic applications.
4. Check Valves
- Prevent backflow in cryogenic pipelines, ensuring unidirectional flow.
- Essential in LNG transportation, oxygen distribution, and hydrogen refueling stations.
5. Butterfly Valves
- Lightweight and compact design for large-diameter piping systems.
- Provide fast operation and precise flow regulation.
- Common in cryogenic fuel delivery systems and industrial gas pipelines.
6. Cryogenic Control Valves
- Automatically regulate gas flow and pressure.
- Used in automated cryogenic processes, aerospace applications, and chemical industries.
Key Features of Cryogenic Valves
For cryogenic valves to perform reliably, they must include specialized design elements:
- Extended Bonnet Design: Protects stem seals from freezing and maintains functionality.
- Low Emission Sealing: Prevents gas leaks, reducing environmental impact and product loss.
- Pressure Relief Mechanisms: Ensures safety by preventing over-pressurization and catastrophic failure.
- Material Durability: Constructed from stainless steel, bronze, or special alloys to withstand extreme cold.
- Fire-Safe & Anti-Explosion Features: Critical for flammable cryogenic gases like LNG and hydrogen.
Essential Cryogenic Accessories
To optimize the safety and efficiency of cryogenic systems, additional components and accessories play a vital role:
1. Pressure Regulators
- Maintain consistent gas pressure in cryogenic distribution systems.
- Prevent pressure spikes that could damage storage tanks and equipment.
2. Safety Relief Valves
- Protect against over-pressurization by automatically releasing excess gas.
- Required by safety standards in LNG plants, medical oxygen systems, and hydrogen storage.
3. Cryogenic Hoses and Fittings
- Flexible yet durable to handle low-temperature liquid transfers.
- Designed to prevent leaks and frost buildup in demanding environments.
4. Vacuum Insulated Piping (VIP)
- Reduces heat loss during liquid gas transfer.
- Commonly used in cryogenic laboratories, semiconductor manufacturing, and space exploration.
5. Filters and Strainers
- Remove impurities from cryogenic gas streams.
- Enhance equipment longevity by preventing debris from entering critical components.
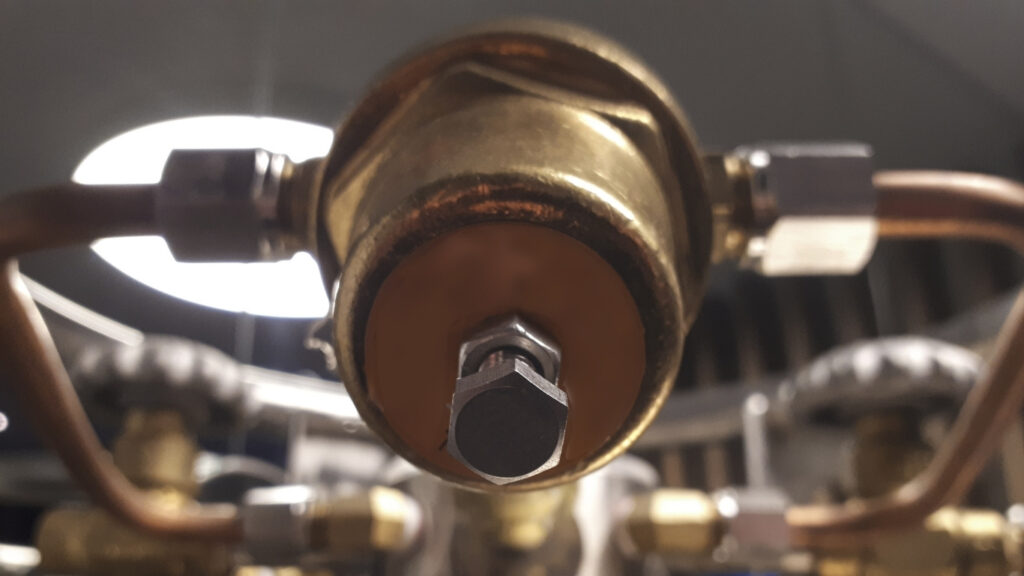
Innovations in Cryogenic Valve Technology
The cryogenic industry continues to evolve with new advancements in valve and accessory technology. Key innovations include:
- IoT-Enabled Smart Valves: Real-time monitoring and remote control of cryogenic systems.
- Self-Heating Valve Technology: Prevents freezing issues without requiring external heat sources.
- Enhanced Leak Prevention: New sealing materials and designs reduce product loss and emissions.
- AI-Powered Predictive Maintenance: Data-driven insights help prevent unexpected valve failures and optimize maintenance schedules.
- Compact, Lightweight Designs: Advanced materials allow for reduced weight without compromising strength and durability.
Reliable Cryogenic Solutions from KAF Cryogenics
Cryogenic valves and accessories play a critical role in ensuring safety, efficiency, and precision across industries like healthcare, aerospace, energy, and industrial gas production. With continued advancements in material science and engineering, modern cryogenic valves offer improved performance, reduced maintenance, and enhanced safety features.
At KAF Cryogenics, we specialize in providing high-performance cryogenic valves and accessories designed for extreme conditions. Our products are engineered to ensure accurate flow control, durability, and safety compliance across various applications.
Explore our range of cryogenic valves, fittings, and accessories on our Products Page, or contact us today to find the right solution for your needs!