Cryogenic Applications in the Automotive Industry
Driving Innovation with Sub-Zero Technology
In the pursuit of efficiency, performance, and environmental sustainability, the automotive industry continuously seeks out groundbreaking technologies. One such innovation making a quiet yet powerful impact is cryogenics. From enhanced material properties to next-generation propulsion systems, cryogenic applications are transforming the way vehicles are designed, manufactured, and powered. This comprehensive guide explores the evolving role of cryogenics in the automotive sector, shedding light on its scientific foundations, practical uses, and potential to drive the future of mobility.
The Fundamentals of Cryogenics in Automotive Applications
What is Cryogenics?
Cryogenics refers to the science of producing and maintaining extremely low temperatures, typically below -150°C (-238°F). It involves the use of liquefied gases such as:
- Liquid nitrogen (LN2)
- Liquid oxygen (LOX)
- Liquid helium (He)
- Liquid hydrogen (LH2)
These substances are used to cool, freeze, or store materials in applications where standard refrigeration methods are inadequate.
Why Cryogenics for Automotive?
Cryogenic technology offers several advantages for the automotive industry:
- Enhanced material durability through cryogenic treatment
- Efficient energy storage with liquid hydrogen fuel
- Superior machining precision during manufacturing
- Low-temperature testing for extreme-condition reliability
Cryogenic Material Treatment in Auto Parts
Deep Cryogenic Processing (DCP)
Cryogenic treatment is used to enhance the strength and wear resistance of metal automotive components. This process involves cooling parts to cryogenic temperatures and holding them there for several hours.
Benefits of Cryogenic Processing:
- Improved fatigue life
- Reduced internal stresses
- Increased hardness and strength
- Enhanced resistance to wear and corrosion
Commonly Treated Components:
- Engine blocks
- Brake rotors and pads
- Transmission gears
- Bearings and crankshafts
- Suspension parts
How It Works:
- Slow cooling to -196°C (using LN2)
- Soaking phase (holding the component at cryogenic temperatures)
- Controlled return to room temperature
Cryogenic Machining in Manufacturing
Cryogenic machining involves using cryogenic fluids like liquid nitrogen as a coolant during the cutting and shaping of automotive parts.
Advantages Over Conventional Coolants:
- Eco-friendly (no harmful chemicals or oils)
- Better surface finish
- Longer tool life
- Improved dimensional accuracy
Applications in Auto Manufacturing:
- CNC machining of aluminum and titanium parts
- Precision shaping of electric motor components
- Cutting high-performance steel alloys
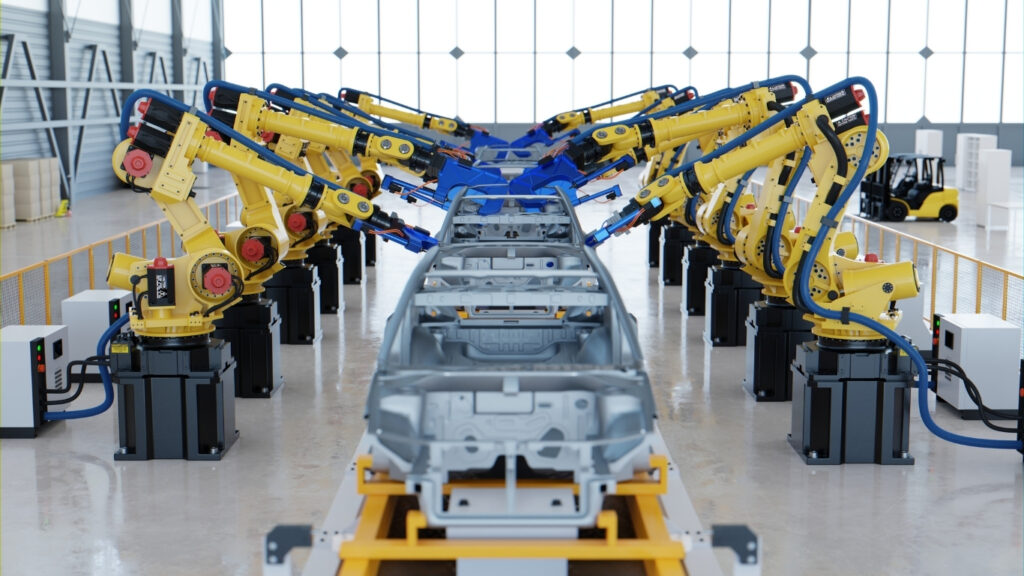
Hydrogen as a Cryogenic Fuel
The Role of Liquid Hydrogen
As the industry shifts toward zero-emission vehicles, liquid hydrogen (LH2) is gaining prominence as a clean fuel alternative.
Key Benefits:
- High energy density per mass
- Zero emissions at point of use (only water vapor)
- Fast refueling times compared to battery-electric vehicles
Cryogenic Challenges with LH2:
- Requires advanced vacuum-insulated tanks
- Sensitive to boil-off losses
- Needs temperature control systems to keep hydrogen below -253°C
Hydrogen Fuel Cell Vehicles (FCEVs):
Automakers like Toyota and Hyundai are investing in FCEVs that use cryogenic storage to power fuel cells:
- Toyota Mirai
- Hyundai Nexo
- BMW Hydrogen 7 (prototype)
Automotive Testing Under Extreme Conditions
Low-Temperature Performance Testing
Cryogenic environments are used to test how automotive components behave under freezing conditions:
Systems Tested:
- Battery performance in EVs
- Fluid dynamics of engine oils and coolants
- Sealing systems under thermal contraction
- Material brittleness at sub-zero temperatures
Benefits of Cryogenic Testing:
- Predict failures in real-world cold climates
- Ensure cold-start reliability
- Validate safety systems under freezing stress
Cold Chain Logistics and Cryogenic Transport
The automotive industry also benefits from cryogenic transport in logistics:
- Cryogenic trucks used for long-distance transport of temperature-sensitive materials (e.g., lithium-ion cells, polymers)
- On-site cryogenic storage for manufacturing plants
Future Trends and Innovations
Electrification and Hydrogen Integration
Cryogenic hydrogen storage systems are being developed for:
- Heavy-duty trucks and buses
- Fleet vehicles
- High-performance motorsports
Smart Cryogenic Systems
- Real-time temperature and pressure monitoring
- AI-driven fuel management
- Integration with onboard vehicle diagnostics
Lightweight Insulation Materials
Advancements in materials science are improving cryogenic insulation:
- Aerogels
- Multi-layer vacuum insulations
- Composite foam barriers
KAF Cryogenics: Empowering Automotive Excellence
At KAF Cryogenics, we understand the unique challenges faced by the automotive industry when implementing cryogenic technologies. Our specialized solutions include:
- Custom-designed cryogenic storage systems
- Advanced liquid nitrogen supply systems
- Deep cryogenic treatment services
- High-efficiency insulation components
Partner with us to integrate precision-engineered cryogenic innovations into your automotive processes. Contact our experts today to learn more about how we can enhance your performance and sustainability goals.
Cooling the Engines of Tomorrow
From high-performance components to clean propulsion, cryogenics is steering the automotive industry into a new era. As sustainability, efficiency, and innovation become driving forces, cryogenic applications offer a transformative edge. Whether it’s boosting the longevity of a brake rotor or fueling a hydrogen-powered sedan, the science of extreme cold is warming up the future of mobility.
Stay ahead with cutting-edge solutions. Trust KAF Cryogenics to keep your automotive operations running at peak performance — even in the coldest conditions.