Level Gauges in Cryogenic Tanks: Ensuring Precision and Safety
The Critical Role of Level Gauges in Cryogenic Storage
Cryogenic tanks are essential for storing and transporting liquefied gases like nitrogen, oxygen, argon, and LNG at extremely low temperatures. These tanks require highly specialized monitoring systems to ensure operational safety and efficiency. One of the most critical components in cryogenic storage systems is the level gauge, which provides real-time data on the amount of liquid inside the tank. Accurate level measurement is vital to prevent overfilling, product loss, and operational hazards.
In this article, we will explore the different types of cryogenic level gauges, their working principles, key advantages, challenges faced in cryogenic applications, and how to choose the best level gauge for your system.
Understanding the Functionality of Cryogenic Level Gauges
Cryogenic level gauges operate using different measurement techniques depending on the application and type of gas being stored. Since cryogenic liquids exist at extremely low temperatures, conventional level measurement methods may not function properly due to ice formation, pressure variations, and material contraction. Level gauges must be designed to withstand these conditions while providing precise and reliable readings.
Some gauges work through mechanical movement, while others rely on electronic or radio wave-based measurements. The selection of the appropriate gauge depends on the specific requirements of the storage system, such as tank size, temperature variations, and the type of cryogenic liquid stored.
Types of Level Gauges Used in Cryogenic Tanks
Several types of level gauges are commonly used in cryogenic applications. Each has its advantages and limitations, depending on the operational requirements.
1. Float-Type Level Gauges
- Operate using a buoyant float that moves with the liquid level.
- Common in small to medium-sized cryogenic tanks.
- Provide reliable, mechanical readings but may require periodic calibration.
- Simplicity makes them cost-effective but less accurate for large storage applications.
2. Differential Pressure (DP) Level Gauges
- Measure the pressure difference between the liquid and gas phases in the tank.
- Suitable for larger storage tanks where precision is critical.
- Offer continuous level monitoring with high accuracy.
- Require careful calibration and maintenance to compensate for pressure fluctuations.
3. Capacitive Level Gauges
- Utilize changes in capacitance to determine liquid level.
- Provide high precision but require specific calibration for each gas type.
- Work well in extreme conditions but may be sensitive to contamination.
4. Radar Level Gauges
- Use microwave signals to detect liquid levels without direct contact.
- Highly accurate and reliable for large cryogenic tanks.
- Not affected by temperature, pressure, or gas composition changes.
- Increasingly popular due to their non-invasive nature and low maintenance.
5. Ultrasonic Level Gauges
- Employ sound waves to measure liquid levels.
- Non-invasive and ideal for tanks where direct contact is not preferable.
- Sensitive to environmental factors like vapor density and condensation.
- Often used in LNG storage facilities and bulk gas storage.
The Importance of Accurate Level Measurement
Properly functioning level gauges are critical for:
- Safety Compliance: Preventing over-pressurization and ensuring adherence to industry regulations.
- Operational Efficiency: Reducing product loss and improving inventory management.
- Accurate Monitoring: Providing real-time data for process control and automation.
- Equipment Protection: Preventing tank damage due to overfilling or excessive pressure buildup.
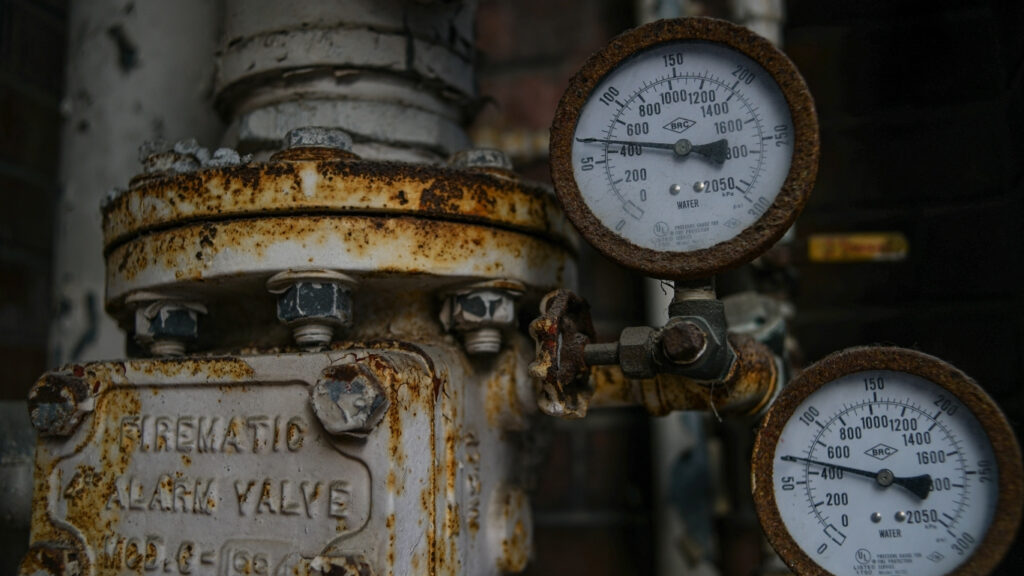
Overcoming Challenges in Cryogenic Level Measurement
Due to the extreme temperatures in cryogenic storage, level measurement presents unique challenges:
- Frost and Ice Formation: Can interfere with sensor readings, particularly for ultrasonic and capacitive gauges.
- Vaporization Effects: Sudden temperature changes may impact accuracy, especially for differential pressure gauges.
- Material Selection: Sensors must be made of materials that can withstand extreme cold without degradation.
- Calibration Complexity: Some level gauges require regular calibration to maintain accuracy.
- Environmental Interference: Radar and ultrasonic gauges may experience signal disruptions in certain conditions.
Selecting the Right Level Gauge for Your Cryogenic System
Choosing the best level gauge depends on several factors:
- Tank Size and Design: Larger tanks may require non-contact measurement methods like radar or ultrasonic.
- Type of Cryogenic Liquid: Some gauges require specific calibration for different gases.
- Environmental Conditions: Factors like temperature fluctuations, frost, and vapor pressure should be considered.
- Required Accuracy and Sensitivity: Some applications require extremely precise measurements, while others can tolerate minor variations.
- Maintenance and Longevity: Some gauges, like float-type gauges, require more frequent maintenance than others.
Innovations Shaping the Future of Cryogenic Level Measurement
With advancements in sensor technology, new trends are shaping the future of cryogenic level measurement:
- Wireless Monitoring Systems: IoT-based remote monitoring allows for real-time data collection without the need for manual checks.
- AI-Enhanced Predictive Analytics: Advanced data analytics can predict potential failures and optimize inventory management.
- Non-Invasive Sensors: New sensor technologies aim to improve accuracy without requiring physical contact with the liquid.
- Self-Calibrating Level Gauges: Smart systems that auto-adjust to environmental conditions for improved accuracy.
Advanced Cryogenic Level Measurement Solutions by KAF Cryogenics
Level gauges in cryogenic tanks play a vital role in maintaining safety, accuracy, and efficiency in storage and transportation. With advancements in technology, newer methods such as radar and ultrasonic level measurement are becoming increasingly popular for their precision and reliability. Selecting the appropriate level gauge ensures seamless operations, minimizes risks, and maximizes product utilization in cryogenic applications.
At KAF Cryogenics, we offer a wide range of high-quality cryogenic level measurement solutions to meet the needs of various industries. Our products are designed for accuracy, reliability, and durability in extreme cryogenic conditions. Whether you need radar, capacitive, or differential pressure level gauges, we have the expertise and technology to help optimize your cryogenic system.
Visit our Products Page to explore our full range of cryogenic storage and measurement solutions, or contact us today to discuss your specific requirements!