Introduction to Cryogenic Manufacturing
Cryogenic manufacturing refers to the production, distribution, and handling of materials, equipment, and systems designed to operate at extremely low temperatures, typically below -150°C (-238°F). These ultra-cold conditions are essential for preserving gases in liquid form, facilitating efficient storage and transportation in industries such as healthcare, aerospace, energy, and industrial gas supply.
At KAF Cryogenics, we are dedicated to providing high-quality cryogenic solutions, including the manufacture, procurement, and distribution of cryogenic pressure vessels, liquid cylinders, storage and transportable tanks, and microbulks. We collaborate with renowned international suppliers who meet stringent global certification standards, ensuring that every product we deliver meets the highest industry benchmarks.
The Significance of Quality Standards in Cryogenic Manufacturing
Quality standards in cryogenic manufacturing serve as essential guidelines that guarantee the safety, efficiency, and longevity of cryogenic equipment. Given the nature of cryogenic materials, any failure in storage or transport can result in hazardous leaks, pressure bursts, or system malfunctions. By adhering to globally recognized quality standards, manufacturers and suppliers mitigate risks, improve product performance, and ensure regulatory compliance across different markets.
At KAF Cryogenics, we work exclusively with certified suppliers and manufacturers to ensure our customers receive products that meet or exceed international safety and performance standards. Our partnerships are based on rigorous evaluation processes, ensuring that only the most reliable and durable cryogenic equipment reaches our customers.
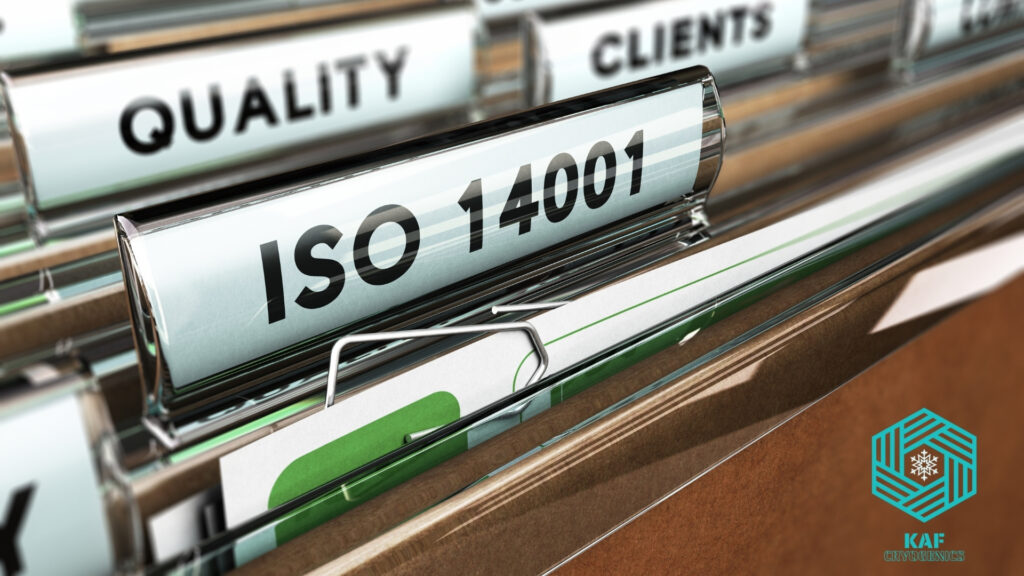
Key Industry Standards Governing Cryogenic Manufacturing
Several international standards regulate the manufacturing and distribution of cryogenic equipment. These guidelines ensure that all components are designed to withstand extreme temperatures and pressures while maintaining operational integrity.
1. Pressure Equipment Directive (PED)
The Pressure Equipment Directive (PED) 2014/68/EU is a European regulation that guarantees the safety of pressure vessels, including cryogenic tanks and storage systems. It outlines the necessary design, testing, and compliance measures for pressure-containing components, preventing failures due to overpressure or material fatigue.
2. EN 13458 – Cryogenic Vessels for Liquefied Gases
This European standard specifies the requirements for the design and manufacture of stationary, transportable, and vacuum-insulated cryogenic vessels. It ensures that these containers maintain their structural integrity, thermal efficiency, and operational safety under extreme cryogenic conditions.
3. ISO 24490:2016 – Cryogenic Pumps Standard
The ISO 24490:2016 standard sets performance and safety guidelines for pumps used in cryogenic applications. Properly manufactured cryogenic pumps facilitate the efficient transfer of liquefied gases without risks of leaks, cavitation damage, or operational failures.
4. ASME Boiler and Pressure Vessel Code (BPVC) – Section VIII
The ASME BPVC Section VIII provides comprehensive guidelines for the design, testing, and inspection of pressure vessels, including cryogenic tanks. Compliance with this standard ensures structural durability, operational safety, and long-term reliability.
5. DOT & UN Standards for Cryogenic Transport
For cryogenic equipment used in transportation, compliance with U.S. Department of Transportation (DOT) and United Nations (UN) transport regulations is crucial. These standards govern the safe handling and movement of liquefied gases across different regions, ensuring accident prevention and legal compliance.
How KAF Cryogenics Ensures Compliance with Quality Standards
At KAF Cryogenics, we take a multi-faceted approach to quality assurance by combining in-house manufacturing excellence with strategic procurement from internationally certified suppliers. Our quality control measures include:
- Stringent Supplier Evaluation: We partner with globally recognized suppliers that hold ISO, ASME, PED, and EN certifications, ensuring that our sourced products meet the highest industry standards.
- Material Selection: We use only high-grade stainless steel, aluminum alloys, and advanced insulation materials that are specifically designed for cryogenic applications. These materials offer superior thermal resistance, minimal thermal expansion, and corrosion resistance.
- Advanced Welding & Fabrication: Our production process incorporates state-of-the-art TIG (Tungsten Inert Gas) welding techniques, ensuring leak-proof, durable joints for cryogenic tanks and vessels.
- Comprehensive Testing Procedures: Every product—whether manufactured in-house or sourced from our partners—undergoes hydrostatic pressure tests, vacuum integrity tests, non-destructive examinations (NDE), and thermal performance analysis to guarantee durability and safety.
- Compliance Documentation & Certifications: We provide full certification and traceability for all our cryogenic products, ensuring compliance with PED, EN 13458, ISO 24490, ASME BPVC, and DOT/UN regulations.
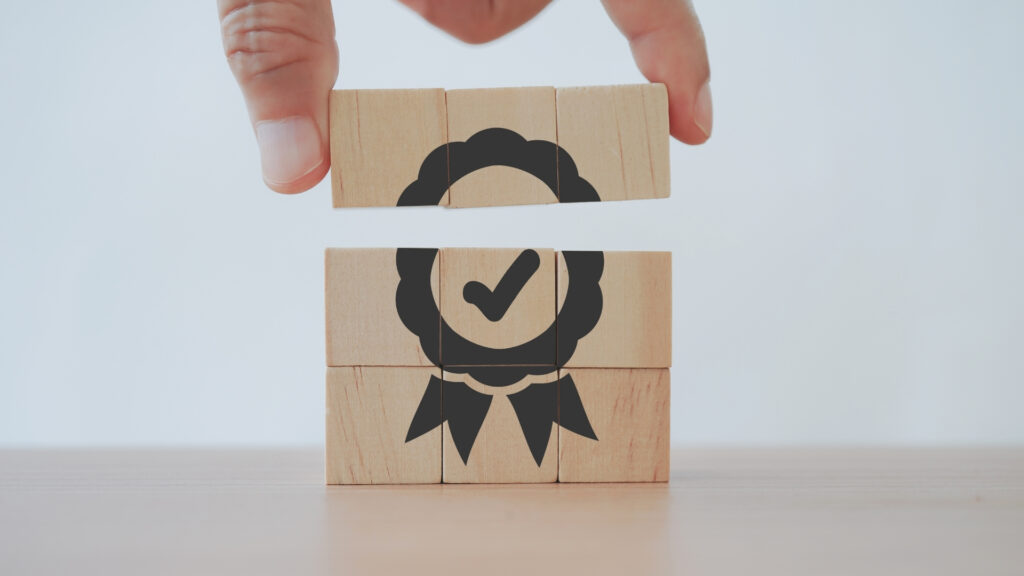
Benefits of Adhering to Quality Standards in Cryogenic Manufacturing
1. Ensures Safety and Reliability
Strict adherence to global standards reduces the risk of system failures, leaks, and operational hazards associated with cryogenic materials.
2. Enhances Product Longevity
High-quality materials and superior engineering techniques ensure that cryogenic tanks, cylinders, and transportable vessels maintain optimal performance over extended lifespans.
3. Facilitates Global Market Compliance
By complying with international regulations, our products can be seamlessly integrated into global supply chains, making distribution easier and reducing legal hurdles in different regions.
4. Strengthens Customer Trust and Satisfaction
Industries that rely on cryogenic solutions demand certified and high-quality equipment. Our commitment to industry standards reinforces credibility, reliability, and long-term client partnerships.
Challenges in Maintaining Quality Standards
Ensuring high-quality standards in cryogenic manufacturing involves several challenges:
- High Material & Production Costs: Premium-quality cryogenic materials and advanced fabrication techniques add to overall expenses.
- Complex Engineering Requirements: Cryogenic systems require precise calculations, specialized manufacturing processes, and strict adherence to international standards.
- Evolving Regulatory Landscape: Industry standards are regularly updated, requiring manufacturers and suppliers to continuously improve and adapt to new requirements.
At KAF Cryogenics, we address these challenges through continuous innovation, investment in advanced technologies, and strict adherence to evolving regulatory standards.
Quality standards are essential in cryogenic manufacturing, ensuring that storage tanks, transportable cylinders, and cryogenic vessels operate safely, efficiently, and reliably. By following internationally recognized guidelines such as PED, EN 13458, ISO 24490, ASME BPVC, and DOT/UN standards, manufacturers and suppliers can deliver world-class cryogenic solutions.
At KAF Cryogenics, our commitment to in-house manufacturing excellence and partnerships with high-quality, certified suppliers enables us to provide top-tier cryogenic solutions. Whether you need cryogenic pressure vessels, liquid cylinders, microbulk tanks, or storage solutions, we ensure that every product meets the highest performance and safety standards.
For more information about our cryogenic products and quality commitment, visit KAF Cryogenics.